At present, the servo press adopts a toggle mechanism, a multi-link, a differential gear train, a worm gear and the like in addition to a conventional mechanism such as a crank connecting rod and a screw nut for large-scale application, and serially connects these basic mechanisms. Or parallel combination design. The servo presses that are widely used in China are mainly the first two structures from the drive structure. This paper analyzes and compares the crank-link and screw nut transmission structures of the main applications in China, and explains the application of the servo press that has been introduced and put into production at present, and the advantages and current development of the servo press. The main problems encountered in the process are discussed for reference and reference by relevant design and production personnel.
First, the structure of the servo press
1. CNC press drive system servoization
The monotonous production method of mechanical presses will not be able to meet the needs of individualized multi-variety and small-volume production, and must follow the path of flexible production. Firstly, the fixed stroke should be changed and the flywheel should be used as the rigid drive mode, and the flexible mode with adjustable stroke amount, stroke dead point and speed can be adapted to the stamping of different types of parts, including stroke curve, speed and workpiece. The forming method and the like are brought close to the optimum forming conditions. Secondly, the flywheel and the clutch are eliminated, and the high-torque heavy-duty servo motor is used to rotate or swing the gear through the gear or directly drive the crankshaft, so that the slider can be combined into various motion modes, which is the advantage of the servo press.
2. Crank and link structure
The eccentric rotating mechanism is driven by a servo motor, and the eccentric rotating mechanism is transmitted to the slider through the connecting rod (see FIG. 1). By continuously rotating the servo motor, the slider can be driven up and down at high speed, which makes it suitable for high-speed production. This type of servo press is simple in structure, easy to develop, eliminates flywheels, clutches and brakes, and reduces gears. It is a pre-selected solution for servo machine presses. It is the servo drive transmission structure preferred by many domestic enterprises, but the machine has the disadvantage of long transmission chain and difficult transmission accuracy. Because the reduction ratio is not large enough and there is no force-increasing structure, the solution has higher requirements on the capacity of the servo motor, which greatly increases the cost. However, due to the crank structure, the motor does not need to complete the forward and reverse movements. At present, the internationally mainly uses Schuler, Huitian, domestic Yiji, Yizhong and other manufacturers to apply this structure. At present, Jinan No. 2 Machine Tool has successfully developed this type of 25000kN large servo press.
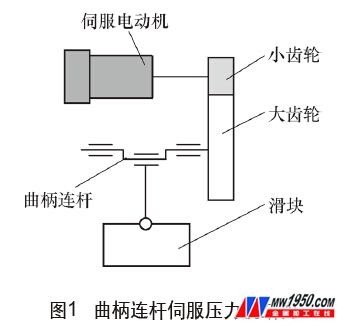
3. Screw nut structure
The servo motor rotary power is used to drive the slider up and down through the toggle mechanism by a ball screw mechanism. In the servo press, an actual position gain conversion formula with respect to a slider position based on a relationship between a slider position, a ball screw position, or a nut position is stored in advance, and when the slider is actually controlled, according to the actual position gain described above The conversion formula corresponds to the slider position correction position gain, and the servo motor speed command is calculated by the slider position deviation and the corrected position gain to control the servo motor. According to this servo press, the slider can be positioned with high precision, and it is suitable for high-precision machining. At present, manufacturers that have been used in production include Japanese Nets, Komatsu and other manufacturers. The utility model has the characteristics of small power consumption of the motor and high transmission efficiency. FIG. 2 is a symmetrical toggle-bar structure servo press used by the Japanese mesh company. The transmission structure of the press has a symmetrical working load on the bed, and the work is stable. Maintain the accuracy of the press for a long time.
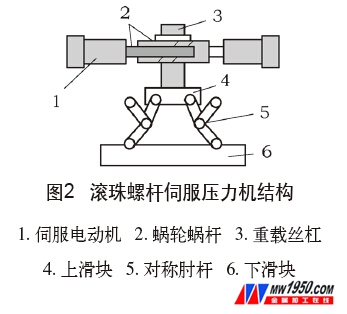
The servo motor drives the worm wheel through the worm, and then moves the slider by the rotation of the heavy-duty screw and the worm wheel, and then uses the symmetrical toggle mechanism to increase the force and then drives the lower slider to move up and down. Due to the use of two servo motor drives, worm gear reduction, and symmetrical toggle force, the toggle mechanism has a simple structure and high rigidity. The toggle mechanism itself has a quick return characteristic, which can well adapt to the forming requirements; The mechanism slider has better low-speed motion characteristics during the working stroke; the toggle mechanism has a good boosting characteristic, which can reduce the control of the servo motor and reduce the power demand of the motor to save energy. The toggle mechanism contains more rotating pairs, and these rotating pair frictions have a greater impact on the triangular toggle mechanism, especially in large servo presses.
The problem with this solution is that the design, efficiency, life, manufacturing and cost of the heavy-duty screw must be solved; the longer the drive chain increases the complexity of the manufacturing; the stroke of the upper slider is much larger, thus increasing The length of the lead screw reduces the punching frequency, so the number of strokes per unit time of the equipment is not large, which restricts the large-scale promotion of the automatic press line.
Second, the servo press characteristics
The servo press adopts the functions of power, shifting and execution of the permanent magnet servo motor, and the controllability of the rotating speed. The driving mechanism is driven directly (or by gear transmission), and the adaptive torque control technology and computer are adopted. Control technology, using digital technology (and feedback control technology) to control the operation of the servo motor, can accurately control the position of the slider relative to the motor corner, in order to independently control the position and speed of the slider, using a stamping mechanism to achieve more The most suitable slider motion mode set by the stamping process, through the preparation of different programs, to achieve various slider motion curves required by the process, to obtain different workpiece deformation speeds, to ensure the quality of the workpiece, and to improve the life of the mold, It is an environmentally-friendly and energy-saving press that realizes the digital control of mechanical presses, making mechanical presses truly enter the digital age.
The main feature of the servo-driven press is that the main drive motor and the slider drive are directly connected to replace the inertia flywheel. Compared with the conventional press, the specific characteristics of the servo press are as follows (see Figure 3).
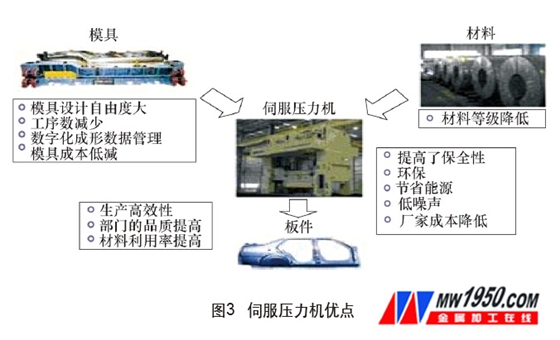
(1) Increasing the productivity The stroke length can be set to the minimum necessary for production, and the forming speed suitable for the processing content can be maintained.
(2) The high precision of the product is controlled by closed-loop feedback, and the bottom dead center accuracy is always guaranteed. Inhibit the product from burrs and prevent the occurrence of defective products.
(3) Low noise, long die life through low noise mode (ie reducing the contact speed between the slider and the sheet), significantly reducing noise compared to general mechanical presses. And the mold vibration is small and the life is long.
(4) Controllability of slider movement Users can use this feature to develop a slider movement mode suitable for the machining process, effectively improve product accuracy and stability, improve mold life and productivity, and achieve silent punching and even It can enlarge the processing range (such as magnesium alloy stamping processing, etc.), suitable for punching, drawing, embossing and bending processes, as well as different material characteristics. If the slider can be stopped and kept pressure, the purpose is to improve the forming quality of the workpiece.
(5) Energy saving and environmental protection canceled the energy-consuming components such as flywheels and clutches of traditional mechanical presses, reduced the driving parts, simplified the mechanical transmission structure; the amount of lubricating oil was small, the stroke was controllable; and the operating cost was also large due to less power consumption. reduce.
Third, the flexible application of servo press
The servo press is driven by a high-power servo motor, which not only improves the material utilization rate, but also improves the product quality. The impact on the mold is reduced, and the life of the mold is greatly improved, thereby saving the development cost of the tooling. In 2007, our company plans to invest in a press line, and finally selected the mesh screw nut servo press structure of Nete. After the acceptance of the equipment, the pressurization process of the servo press was studied. From the analysis of stamping process, the main advantages of servo press are: improve the material utilization rate of the whole vehicle, reduce the purchase cost of the whole vehicle; improve the forming quality and surface quality, can control the precision of the parts well; reduce the impact on the mold The maximum freedom of mold design, while reducing the investment cost of the mold; in the maintenance of the mold and the noise of the environment, the servo press is also much better than the mechanical press.
1. Calculation of servo press work
(1) In order to ensure that the servo press meets the forming force of the part, the work of the servo press is verified in detail in the early stage of equipment selection (see Figure 4): 1 The mechanical press drive part is driven by the motor, reducer, clutch and Main components such as brakes, flywheel mechanisms and linkages. 2 The drive part of the servo press is composed of a main part such as a servo drive motor, a reducer, and a link mechanism. 3 mechanical press work needs to be transmitted to the slider by the rotational inertia energy of the flywheel, and the flywheel decelerates or accelerates to release or store energy, and this part (about 36%) of energy is delivered to the slip through the relevant action of the clutch and brake. The block completes the part forming process. 4 The servo press has no flywheel to store and release energy. The energy required for each stroke of the slider is amplified and supplied to the slider by the servo motor through the link structure. Therefore, the servo press energy is expressed by the actual forming effective work mode.
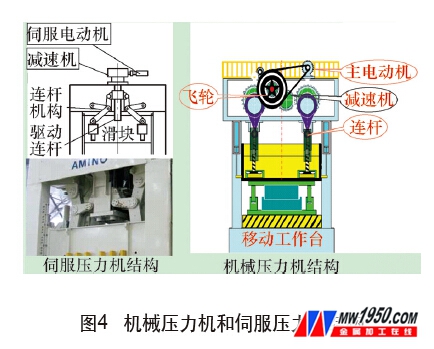
(2) Calculation of work. The F91A double row side wall is the part with the most required press work. Part data: size is 2680mm × 1785mm × 0.8mm, material mechanical grade is DC56D, tensile strength is 260MPa, yield strength is 150MPa. Process parameters: die pad pressure is 1800kN, stretch pad stroke is 180mm, mold nitrogen cylinder maximum pressure is 800kN, stroke is 70mm, part forming depth is 150mm, (2680+1785) mm × 2×0.8mm. According to the above data, the force required to form the part is
F tensile strength = L (circumference) × C (material thickness) × σ b (tensile strength) = (2680 + 1785) × 2 × 0.8 × 10 -6 m 2 × 260 × 10 6 Pa 1857.4 × 10 3 (N)
F yield strength = L (circumference) × C (material thickness) × σ s (yield strength) = (2680 + 1785) × 2 × 0.8 × 10 -6 m 2 × 150 × 10 6 Pa≈ 1071.6 × 10 3 N
Note: F tensile strength is the tensile strength of the material. If it exceeds this value, the part is scrapped, that is, the ultimate force; F yield strength is the yield strength of the material, and the data material begins to undergo plastic deformation to complete the stamping process, that is, the forming force of the part.
The press slider slides down to complete the stamping process. The force to be overcome is the sum of the die pad force, the mold nitrogen cylinder stroke force, and the plastic deformation force of the part. Therefore, the energy required for the press is
W press effective work = FS = W overcome die pad + W mold nitrogen cylinder + W part plastic deformation = 1800 × 10 3 N × 180 × 10 -3 m + 100 × 10 3 N × 70 × 10 -3 m + 1071.6 ×10 3 N×150×10 -3 m=324kJ+70kJ+160.7kJ=554.7kJ
The actual effective power of the 20000kN servo press is ≥560kJ, which fully meets the requirements.
2. Application of servo press
(1) Using servo press flexibility to improve part quality Servo mechanical press has the characteristics of compounding, high efficiency, high precision, high flexibility, low noise and environmental protection, which makes its application in forming process more and more important. The technology of the servo press can be used to optimize the technology and has great process flexibility. There are a variety of slider motion curves. By adjusting the blanking force at different positions of the die pad, the formability of the parts is improved (see Figure 5 and Figure 6). Compared with the external committee, the scrap rate of the parts is reduced, and the parts are improved. The surface quality reduces the repair rate and improves the pass rate of the parts. The annual cost of repairing parts is 208,848 yuan (see Figure 7).
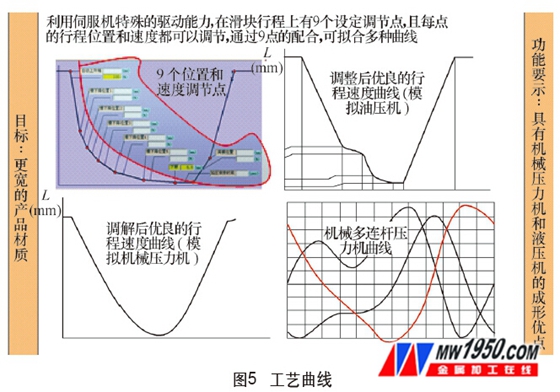
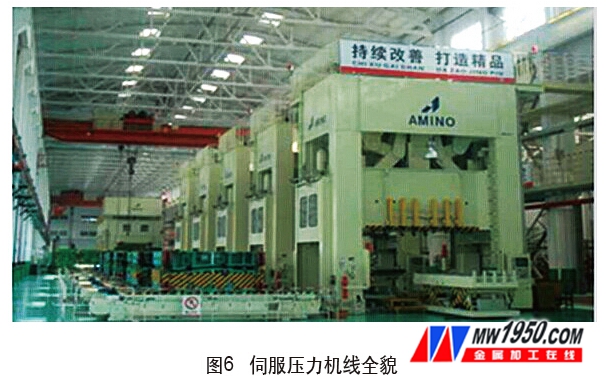

(2) Using the servo press to increase the SPH value. In the ordinary press, the motor load is relatively stable. Even during the non-working period of the working cycle, the flywheel consumes energy to restore the flywheel speed. The energy is consumed in the whole cycle, and the rated power of the motor is basically The upper is equal to the average energy consumption of the cycle. For AC servo drives, there is no flywheel and the actual power consumed is variable. In terms of the rated power of the motor, the servo press will be larger than the normal mechanical press. However, due to the different power consumption of the two driving methods, the actual energy consumption of the servo press is still lower than that of the ordinary press. As can be seen from Figure 8, the servo press line energy consumption is significantly lower than the mechanical press line.
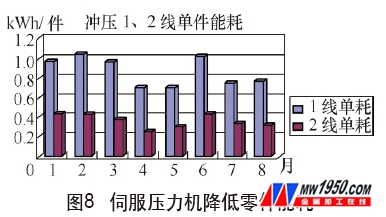
Through the use of servo press technology, the technology can be optimized. For some molds and parts, the height of the part is adjusted properly. By adjusting the stroke of the part, the SPH value of the second line is increased from 180 pieces/h to 210 pieces/h. The total annual output of the servo line needs to reach 900,000 pieces, and the processing time is reduced from the original 5000h to 4285h, which can save 750h labor and electricity costs, and increase the annual income by 1.045 million yuan (see Figure 9).
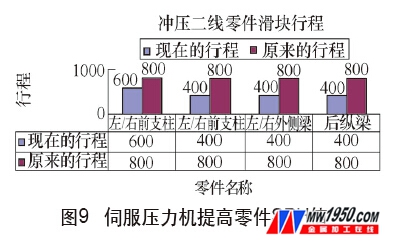
(3) Using the flexible canceling process of the servo press, through the step-by-step understanding of the performance of the servo press, the "cancel the left and right front pillar drop material mold" was improved, and the blanking process was cancelled, and the first order was directly deep-molded during production, which was reduced. Labor costs and energy costs ensure the quality of the part.
At present, the servo press line has a good running effect, the quality of parts is significantly improved compared with the traditional press, and the profit is obviously improved. Compared with the traditional press, the annual benefit is increased by 2,227,670 yuan.
Fourth, summary
1. Advantages and prospects of servo presses
The servo press has many advantages in performance, which has been confirmed. However, there is no consensus on the development prospects of such presses. There is not a consensus in the industry. There are not many countries in the world that have truly achieved commercial production. The transmission mode of the common AC motor + flywheel has a series of advantages such as low cost, simplicity and reliability, and it has good rigidity, reliability and high productivity to serve mass production in various industrial sectors, and has low maintenance cost in later use. Highly economical, we will continue to serve the society with these characteristics. It is foreseeable that it is not necessary or possible to use servo drives for all presses in the future. However, servo drives bring a series of advantages to the press, especially the advantages of flexibility and energy saving and noise reduction show attractive prospects for forging equipment.
2. Transformation of traditional mechanical presses
Another solution is to modify the traditional mechanical press, but the required motor static torque value will be 7-8 times larger than the original ordinary motor power, although the slider motion state can be fully controlled by the motor and the motor itself. Intermittent work specifications, but mechanical and electrical structure design is difficult, equipment investment is too difficult to push to the market, the current DDC technology promoted by ABB, to a certain extent can improve the flexibility of mechanical press.
3. Kinetic energy recovery for moving parts
The servo press uses electromagnetic braking, and the kinetic energy of the moving parts is converted into electric energy. If this part of the electric energy cannot be recovered, it will reduce the efficiency through the resistance consumption, and increase the resistance box and the cooling system. The energy recovery uses the following three methods.
(1) Feedback grid Although this method can save energy, it needs to add a set of inverter system, which increases the cost.
(2) Capacitor storage Add a set of large-capacity capacitors in the drive circuit, store the electric energy generated when the motor brakes, and release it for use when the motor is used for stamping. This solution not only saves electricity, but also greatly reduces the impact on the power grid (about 80 %). The disadvantage is that large-capacity capacitors are expensive and very bulky.
(3) Multi-machine DC interconnection If there are multiple presses working in the workshop at the same time, it can be considered to be connected to the DC layer in the drive circuit, which can also achieve the effect of energy saving and peak current leakage, and can also eliminate the inverter and capacitor. This is currently the most economical and cheap solution. At present, this kind of solution has been used in the servo press line introduced by our company.
4. Servo press energy consumption and motor capacity
Since the servo press does not have the flywheel to store energy, it is powered by the main motor when it reaches the bottom dead point of the press. Generally, the main motor power of the servo press is at least 2.5 times higher than that of the equivalent tonnage mechanical press. For this reason, many manufacturers have separate servo presses. The press is equipped with a separate transformer for this purpose, so this is one of the obstacles to the large-volume use of servo presses. One of the ways to reduce the capacity of the motor is to increase the overload capacity of the motor.
The competition in the automotive industry has gradually shifted to product quality and cost competition. Who can produce high-quality cars at a reasonable cost is a key factor in the success of various automobile OEMs in the future. The introduction of new equipment and new technology has promoted the development of the automobile manufacturing industry, and the technological level also reflects the manufacturing level of an automobile main engine factory. The servo press is a third-generation press that is completely different from the traditional mechanical press. It is a combination of information technology, automatic control technology and traditional mechanical technology. The emergence of servo presses has made it possible for the automotive industry to use more new materials, bringing innovation to the automotive stamping process. In the actual selection of equipment, in order to save investment, servo presses can be selected in the first forming process of the press line.
About the author: Zhang Yonggang, Department of Manufacturing Technology, Light Commercial Vehicle Branch, Dongfeng Motor Co., Ltd., engaged in stamping work.
Astm A106 B Seamless Steel Pipe
Astm A106 Gr B Pipe,Astm A106 Pipe,A106 Seamless Pipe,Astm A106 B Seamless Steel Pipe
Liaocheng Xinglong Seamless Tube Manufacturing Co., Ltd. , https://www.lcxlpipe.com