Check the product certification, quality assurance certificate, specification model, variety and quantity of the required fittings, fittings and valves, as well as pipe supports, fasteners, seals, etc., and perform visual inspection
Construction and installation points of pipes
Company Name: Changsha Baoshan Building Materials" target=_blank>Building Materials Trading Co., Ltd.
Changsha baoshan building materials trading co., LTD
Service Hotline
Contact: Pan Baoshan
Address: Baoli Valley, Linyu, Yuelu District, Changsha City
Website: http://
one. The following conditions should be met before installation of the pipeline:
1. The construction drawings and other technical documents are complete, and technical submissions have been made;
2. Check the product certification, quality assurance certificate, specification model, variety and quantity of the required fittings, fittings and valves, pipe fittings, fasteners, seals, etc., and perform visual inspection;
3. The construction site and construction water and power supply meet the requirements;
4. Construction equipment has arrived;
5. The device connected to the pipe is fixed or positioned.
two. Construction personnel should be technically trained, familiar with the performance of steel-plastic composite pipes, and master basic operational skills.
three. The following construction tools should be used for steel-plastic composite pipes:
1. Cutting should use a metal saw;
2. The threading machine should adopt automatic threading machine;
3. The groove should be a special groove groove machine;
4. The elbow should be cold-bent with a bender;
four. Steel-plastic composite pipe construction procedures should meet the following requirements
1. The indoor buried pipe shall be installed before the construction of the underground civil construction floor;
2. The indoor buried pipeline should not be less than 500mm outside the external wall, and the nozzle should be sealed in time;
3. Steel-plastic composite pipes shall not be buried in the reinforced concrete structural layer;
4. Pipe installation should be gradually connected from large diameter to small diameter;
Fives. Pipes crossing the floor, roof, water tank (pool) wall (bottom), should be reserved for holes or pre-embedded casing, and should meet the following requirements:
1. The reserved hole size should be 40mm of the outer diameter of the pipe;
2. When the pipe is darkly laid in the wallboard, the pipe groove width shall be 30 mm of the pipe outer diameter; and the pipe groove slope shall be the pipe slope;
3. Reinforced concrete water tank (pool), waterproofing casing should be pre-buried at the crossing of inlet pipe, outlet pipe, drain pipe, overflow pipe, etc., and waterproof concrete should be embedded and compacted.
six. When the pipe diameter is not more than 50mm, the bending machine can be cold-bent, but the bending radius of curvature should not be less than 8 pipe diameter, and the bending angle should not be greater than 100.
Seven. Pipes buried in the wall and embedded in the wall shall be filled in time after the concealed works are collected.
Threaded connection
one. The pipe cut should meet the following requirements:
1. The sawing pipe should be a sawing machine, and it should not be cut by a grinding wheel. When cutting with a circular saw, its speed shall not exceed 800r/min;
2. When using a hand saw tube, its saw surface should be perpendicular to the tube axis.
two. The thread should meet the following requirements:
1. The threading machine should adopt automatic threading machine;
2. The threading machine should be lubricated with lubricating oil;
3. Conical pipe threads shall comply with the requirements of the current national standard GB/T7306 with threaded pipe ribs and shall be tested by standard thread gauges.
three. Pipe end cleaning processing should meet the following requirements:
1. Apply fine boring to trim the burrs of the metal tube ends;
2. Cotton back and brush should be used to remove oil, water and metal chips from the pipe ends and threads;
3. The lining plastic pipe shall be a special reamer, and the thickness of the lining plastic layer shall be 1/2 chamfered, and the chamfer slope shall be 100~150;
four. After the pipe end and pipe thread are cleaned and processed, anti-corrosion and sealing treatment shall be carried out. It is advisable to use the anti-rust sealant and the raw material tape to wrap the thread, and at the same time, the color pen is used to mark the screwing depth on the pipe wall.
Fives. Non-lined malleable cast iron pipe fittings shall not be used.
six. Before connecting the pipe to the fitting, the rubber seal or anaerobic sealant in the lining malleable cast iron pipe fitting shall be inspected. Then, the fitting is hand-spun on the pipe end thread. After confirming that the pipe fitting interface has been inserted into the lining plastic pipe, the pipe and the pliers are used to connect the pipe to the fitting according to Table 1.
Note: Do not rotate in the opposite direction.
Seven. After the pipe and fittings are connected, the exposed threaded part and all the parts of the clamp and surface damage shall be coated with a rust-proof sealant.
Eight. The pipe joint sealed with anaerobic sealant shall have a curing period of not less than 24 hours, and no pressure test shall be carried out during this period.
nine. The steel-plastic composite pipe shall not be directly connected to the valve, and the special inner and outer threaded transition pipe joints with brass inner lining shall be used.
ten. The steel-plastic composite pipe shall not be directly connected to the water supply pipe, and the special internal threaded pipe joint of brass shall be used.
eleven. When the steel-plastic composite pipe is connected with copper and plastic pipes, a special transition joint should be used.
twelve. When the internal and external thread special transition joints with internal lining are connected with the pipe fittings and accessories of other materials, the anti-corrosion treatment should be taken at the end of the external thread.
Flange connection
one. Flanges for steel-plastic composite pipes shall comply with the following requirements:
1. The convex panel type flat welded steel pipe flange shall comply with the requirements of the current national standard "convex panel type flat welded steel pipe flange" GB/T9119.5~9119.10;
2. Convex necked steel pipe flanges shall comply with the requirements of the current national standard "Convex necked steel pipe flanges" GB/T9114.1~9114.3, only applicable to steel-plastic composites with a nominal pipe diameter of not more than 150mm. Tube connection
3. The pressure rating of the flange should match the working pressure of the pipe.
two. The steel-plastic composite pipe flange field connection shall meet the following requirements:
1. The pipe of steel-plastic composite pipe shall comply with the requirements of 6.2.1 of this regulation;
2. When fitting the flange on site, the inner-lined plastic convex surface with neck threaded steel pipe flange shall be used;
3. The pipe thread for the threaded and sealed thread on the connected steel-plastic composite pipe shall conform to the requirements of the current national standard "Threaded Pipe Thread" GB/T7306;
three. The steel-plastic composite pipe flange connection can be installed once or according to the technical proficiency of the construction personnel:
1. One-time installation method: It can be measured on the spot, draw the single-line processing drawing of the pipeline, send it to the professional factory for the pipe section, after the parts are coated (lining), and then transported to the site for installation;
2. Secondary installation method: Non-coated (lining) steel pipes and fittings can be used on site, flange welded, assembled pipelines, and then removed and transported to a professional processing plant for coating (lining) processing, and then shipped to the site for installation.
four. Flange connection of steel-plastic composite pipe When the secondary installation method is adopted, the pipe sections, pipe fittings, valve parts and flanges installed on the site shall be marked with a steel stamp number. General requirements for threaded flange connection groove connection inspection and acceptance
Inspection and acceptance
one. The experimental pressure of the steel-plastic composite pipe water supply pipe system should be the same as that of the ordinary steel pipe water supply system.
two. The pressure test procedure of the steel-plastic composite pipe system is consistent with the ordinary steel pipe system. When the steel-plastic composite pipe and the plastic pipe are tested in the same system, they shall be carried out in accordance with the relevant standards of the plastic pipe.
three. After the pipeline is pressure tested, the water in the pipeline system should be emptied and the pipeline cleaned. Pipes that transport drinking water should also be disinfected. The water quality of the disinfected pipeline shall comply with the requirements of the current national standard “Standard for Drinking Water†GB5749.
four. The construction water supply steel-plastic composite pipeline project shall be subject to sub-item, division and unit project acceptance according to relevant state regulations. The construction unit shall conduct self-inspection before the intermediate acceptance and completion acceptance. Records should be recorded, signed, and filed at the time of acceptance.
Fives. The following documents should be available for acceptance:
1. Construction drawings, as-built drawings and design change documents;
2. Material certificate and quality assurance certificate;
3. Intermediate test records and concealed project acceptance records;
4. Hydraulic pressure test record and flush water test record;
5. Engineering quality accident record;
6. Sub-item, division, unit engineering quality inspection records.
six. The following items should be checked during project acceptance:
1. Whether the pipe and pipe fittings are consistent with the purpose, and the pipe fittings used for cold water pipes shall not be used for hot water pipes;
2. Whether the pipeline is connected with the valve or the water supply plug, whether the special transition fitting is used;
3. Whether the grooved connection uses a special rubber sealing ring;
4. Whether the number of exposed teeth of the pipe joint is excessive;
5. Whether the outer wall of the pipe in the water tank (pool) is plasticized, whether the support member is firm and anti-corrosive, and the waterproofness and firmness across the wall (bottom);
6. Check the pipe position, pipe diameter, elevation, slope, verticality, support position and firmness;
Anti-corrosion treatment of buried pipelines.
Groove connection
one. The groove connection method can be applied to the connection of coated (lining) plastic steel pipes with a nominal diameter of not less than 65 mm.
two. Grooved pipe joints shall comply with the relevant national product standards.
three. The working pressure of the grooved pipe joint should match the working pressure of the pipe.
four. Grooved pipe joints for conveying hot water should be made of temperature-resistant rubber seals. The rubber material used for drinking water purification pipelines shall comply with the requirements of the current national standard “Safety Evaluation Standard for Drinking Water Distribution Equipment and Protective Materials†GB/T17219;
Fives. For the lining-plastic composite steel pipe, when the groove is installed in the field and the pipeline is installed, the construction shall meet the following requirements;
1. The finished grooved plastic coated pipe fittings should be preferred;
2. The length of the connecting pipe section shall be the net length between the two ports of the pipe section minus 6~8mm, and each joint shall have a gap of 3~4mm and be numbered with a steel stamp;
3. The mechanical pipe shall be used, the section shall be perpendicular to the axis, and the allowable deviation shall be: when the pipe diameter is not more than 100 mm, the deviation is not more than 1 mm; when the pipe diameter is greater than 125 mm, the deviation is not more than 1.5 mm;
4. The end face of the outer wall of the pipe is machined with 1/4 wall thickness rounding;
5. Apply the special groove groove machine to press the groove. When the groove is pressed, the pipe section should be kept horizontal. The steel pipe and the groove groove machine face are 900. The groove should be continuously progressive. The groove depth should meet the requirements of the following table; and the standard gauge measurement groove should be applied. The depth of the week. If the groove is too shallow, the groove machine should be adjusted before processing.
Groove standard depth and tolerance (mm)
Pipe groove depth tolerance
≤802.20+0.3
100——1502.20+0.3
200——2502.50+0.3
3003.0+0.5
Steel-plastic composite pipe use method:
1. For the connection of steel-plastic composite pipe, tools such as hacksaw, boring tool, stranding machine and pipe wrench should be used.
2. The connection method and pipe form are basically the same as those of the traditional galvanized pipe. Generally, the pipe with the diameter of DNl5-100 adopts this connection mode.
3. The joint between the pipeline and the pipe fittings must be wound with the raw material tape to ensure that the entire steel-plastic composite pipe is protected.
4. When cutting, it is not allowed to cut with high-speed method such as high-speed grinding wheel cutting machine and gas cutting. When cutting with a threaded wire, it can only be cut to the wall thickness of the 1/2 steel pipe, and then the pipe saw is broken by hand saw. This method is generally not allowed to be applied, but the hand saw is used for cutting. After cutting, use a tool such as a semi-circular file to remove internal and external burrs.
5, can not be bent by heating method. The cold bend method is applied when the manifold is used, and the bending radius is not less than 6 times the diameter.
6, should be connected with a variety of standard pipe fittings.
7. The surface of the wire mouth interface should be clean.
8. Steel-plastic composite pipes shall not be exposed, contaminated or damaged during transportation.
9. It should be kept in the warehouse where the temperature is not higher than 35 degrees, away from the heat source, and the storage period is 1 year from the date of production.
Product Features:
A. Safety, environmental protection, hygiene, high strength
Outsourcing hot-dip galvanized welded steel pipe, lining polyethylene (PE) and polypropylene (PPR) complying with food hygiene requirements, the steel pipe has high strength, good steel property, high pressure resistance and non-scaling and non-toxicity of plastic pipe. The combination of rust, acid and alkali resistance, frost resistance and heat resistance (-20oc-95oc), smooth inner wall and small flow resistance, the system nominal pressure is 2.5Mpa, which overcomes the fatal defects of steel pipe and plastic pipe when used alone.
B. Bonding technology
The steel-plastic composite pipe is made of imported thermoplastic adhesive between the steel pipe and the plastic pipe for high-temperature bonding, so that the composite bond strength between steel and plastic reaches 4.3Mpa. According to the good toughness and impact resistance of polyethylene (PE). They are superior to UPVC, so the Jinpin steel-plastic composite pipe will not undergo plastic cracking, degumming, steel-plastic separation and the like when it is flattened, bent and gully.
C. Secondary seal
When the pipe is connected with the pipe fitting, in addition to the raw material tape for sealing, a natural silicone rubber pad is placed in the injection pipe fitting, so that the end face of the pipe mouth and the tubular root of the pipe fitting are sealed, so that the pipe fitting is completely isolated from the water, thereby It completely solves the problem of internal corrosion of pipes and fittings and ensures the quality of water supply.
Jin brand steel-plastic composite water pipe application areas:
1, hot and cold drinking pipe system
2, building pure water pipeline system
3. Building fire protection piping system
4, central air conditioning, heating pipe system
5. Chemical production medium conveying pipeline
PPR construction requirements
1 The water pipe uses special hot melt welding.
(1) Cut the pipe using the pipe cutter vertically. When using other tools (such as fine-tooth saws, cutters, etc.) to cut the pipe, remove the burrs at the mouth and mark the hot-melt plug depth at the pipe end with a pen ( 20, 25M depth is about 15MM).
(2) Heating the pipe and pipe fittings When the hot-melt welder is heated to 260 ° C (after the indicator light is on), the pipe and the pipe fittings are simultaneously pushed into the fusion splicer die, and the heating time is not less than 5 seconds.
(3) Connect the pipe fittings to remove the heated pipe fittings at the same time, and insert them into the marked depth quickly, which can be adjusted properly, but it is strictly prohibited to rotate.
(4) Cooling Cool the connected pipe fittings for 3-5 minutes.
Inspection and acceptance
After the installation of the pipeline is completed, a hydraulic test must be carried out to confirm whether the welded state is good, otherwise it is strictly prohibited to hide the pipeline.
Proceed as follows:
1. Seal the end of the pressure test pipe, slowly fill the water, and discharge the gas inside the pipe. After filling with water, check the water seal.
2. The pressure should be slowly boosted by a manual pump, and the boosting time should not be less than 10 minutes.
3. After rising to the specified test pressure (generally 1.0 MPA or more), the pressurization is stopped. Regulate for 1 hour and observe if there is water leakage at the joint.
4. After the voltage is regulated, the pressure is applied to the specified test pressure value, and the pressure drop within 15 minutes is not more than 0.05 MPA.
* At the end of the pressure test, the original pressure test record and the user's signature must be retained.
Bridge and gantry crane safety technical inspection program (special inspection)
The above contents are compiled according to the problems encountered by the students in the actual work, for reference, if there is any problem, please communicate and correct in time.
Http://news.chinawj.com.cn
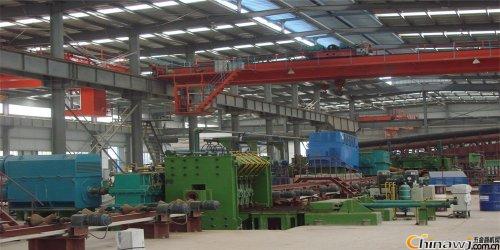
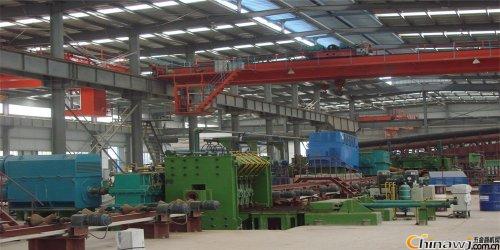
As fine ceramic material's extraordinary physical characteristics, Structural ceramic components is widely used in many different machinery, equipment in varity of different field. They work as support component, connection part, terminal insulator, ceramic body, ceramic shell ,electronics ceramic wafer, engineering tools and so on.
We provide varity of grade high precision ceramic components based on our reliable high precision manufacturing equipment and inspection tools.
Structural Ceramic Component,High Precision Structural Ceramic Component,Zirconia Ceramic Structural Component,Structural Component Ceramic Part Type,Structural Ceramics
Jinghui Industry Ltd. , https://www.ceramictek.com