Particle board, also known as particleboard and Chipboard, is an engineered wood product manufactured from wood chips, sawmill shavings, or even sawdust, and a synthetic resin or other suitable binder, which is pressed and extruded. Oriented strand board, also known as flakeboard, waferboard, or chipboard, is similar but uses machined wood flakes offering more strength. All of these are composite materials that belong to the spectrum of fiberboard products.
* Size : 1220 x 2440 mm 1830 * 2440 mm or as clients requirement
* Thickness : 9 - 30 mm
* Gluing : E2, E1, E0
* Moisture : below 8 %
* Face and Back : plain, melamine faced or veneer faced
* Veneer Species : birch, mahogany, ash, sapele, walnut, teak, oak, maple, beech, cherry, red rose, ect.
* Veneer Grade : A, AA or AAA
What is MDF ?
Wood-based panel manufactured from lignocellulosic fibres by the [dry process", i.e. having a fibre moisture content less than 20% at the forming stage and being essentially produced under heat and pressure with the addition of an adhesive,including Plain MDF Board and Raw MDF Sheet.
How is it made?
* Chipping: The raw material (forest thinnings, sawmill byproducts, etc.) is chipped.
* Reduction to fibres:
The chips are softened by pre-heating in low-pressure steam and then fed by Archimedean screw between segmented grinding discs, one of which rotates at great speed.
* Resin application:
Adhesive, usually urea formaldehyde, and wax emulsion are applied to the fibre within the inlet pipe to the drying tube.
* Drying / storage:
Drying of the fibre/adhesive mix is performed in a long drying tube (blowline). The dry fibre is stored in silos to await further processing.
* Mat forming:
A mattress is dry-formed on caul plates. This is gradually compressed by steel belts. For thick boards, more than one mat may be piled on another.
* Pressing:
The dry mattress is pre-pressed to consolidate it and then cut and formed to press sizes, finally to be cured with heat and pressure in a multi-daylight or a continuous press.
* Trimming and sanding:
After cooling, each panel is trimmed and sanded to precise dimensions.
What is it used for?
Plain boards for a wide range of interior uses are available in Europe with thicknesses in the range of 1,8 to 60 mm.
Unlike most other wood based sheet materials, the uniform and close packed fibre distribution throughout the thickness of MDF allows detailed machining operations to be carried out on the faces and edges without breakout or the exposure of voids within the core of the board.
Standard MDF is being used successfully for the manufacture of table tops, door panels and drawer fronts with moulded edges or profiled surfaces. The smooth and stable surfaces of MDF provide an excellent substrate for painting or the application of decorative foils or wood veneers. The inherent stability, good machinability and high strength of MDF creates opportunities for it to be used as an alternative to solid wood for applications such as drawer sides, cabinet rails, mirror surrounds and mouldings.
Although primarily developed for use in furniture, standard MDF is being used increasingly for shop fitments, exhibition displays, wall panelling, architectural mouldings and many other applications where its good machining and finishing characteristics are used to advantage.
Specifications:
* Thicknesses (mm): 6, 8, 10, 12, 16, 18, 19, 22, 25, 28, 30,
* Size (mm) :1220x2440 mm ,1830x2440 mm, 2200x2800 mm, other sizes on request
* Classification according to the condition of surfaces
* Glue type: Urea Carbamide (Interior)
* Edges: Processing by waterproof acrylic paint
* Formaldehyde emission: E1
* Moisture content: Below 8%
* Density: 680 – 700 kg/m³
* Wood species: Poplar , pine and hardwood combination etc
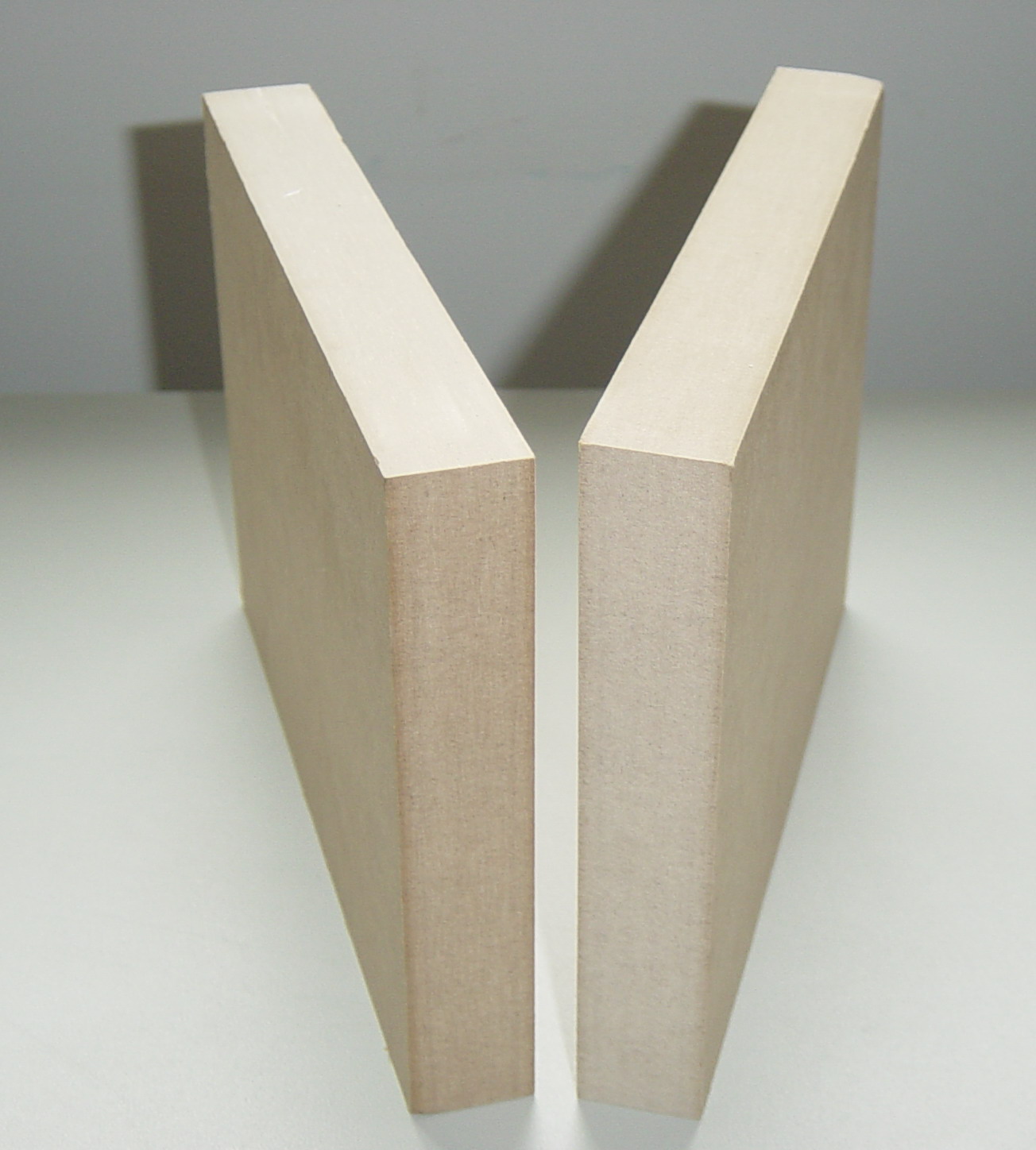
Plain MDF,Plain MDF for Furniture,8mm Plain MDF,Light Color Plain MDF Board,Plain MDF Board,Raw MDF,Raw MDF Sheet
TOTAL WOOD CO ., LTD , http://www.total-woods.com